Precast Fire Resistance Design
Concrete and precast structures are the BEST solution when designing for fire resistance. Precast concrete is non-combustible, helps to contain fires, and continues to provide support to the structure even in intense heat.
Balanced Design and Compartmentation
The Pennsylvania, New England/New York and Mid Atlantic Fire Safe Construction Advisory Councils released a study that discussed the best way to construction multi-residential structures to keep communities safe from fire related events.
The study discussed using a threefold approach to designing fire safe construction which included the following design elements:
- Compartmentation: Using structural walls, floors, and ceilings of masonry and concrete products that provide 2-4 hours of protection with non-combustible materials
- Detection: Use of smoke detectors to alert residents
- Suppression: Use of sprinklers to control the fire until emergency personnel arrive
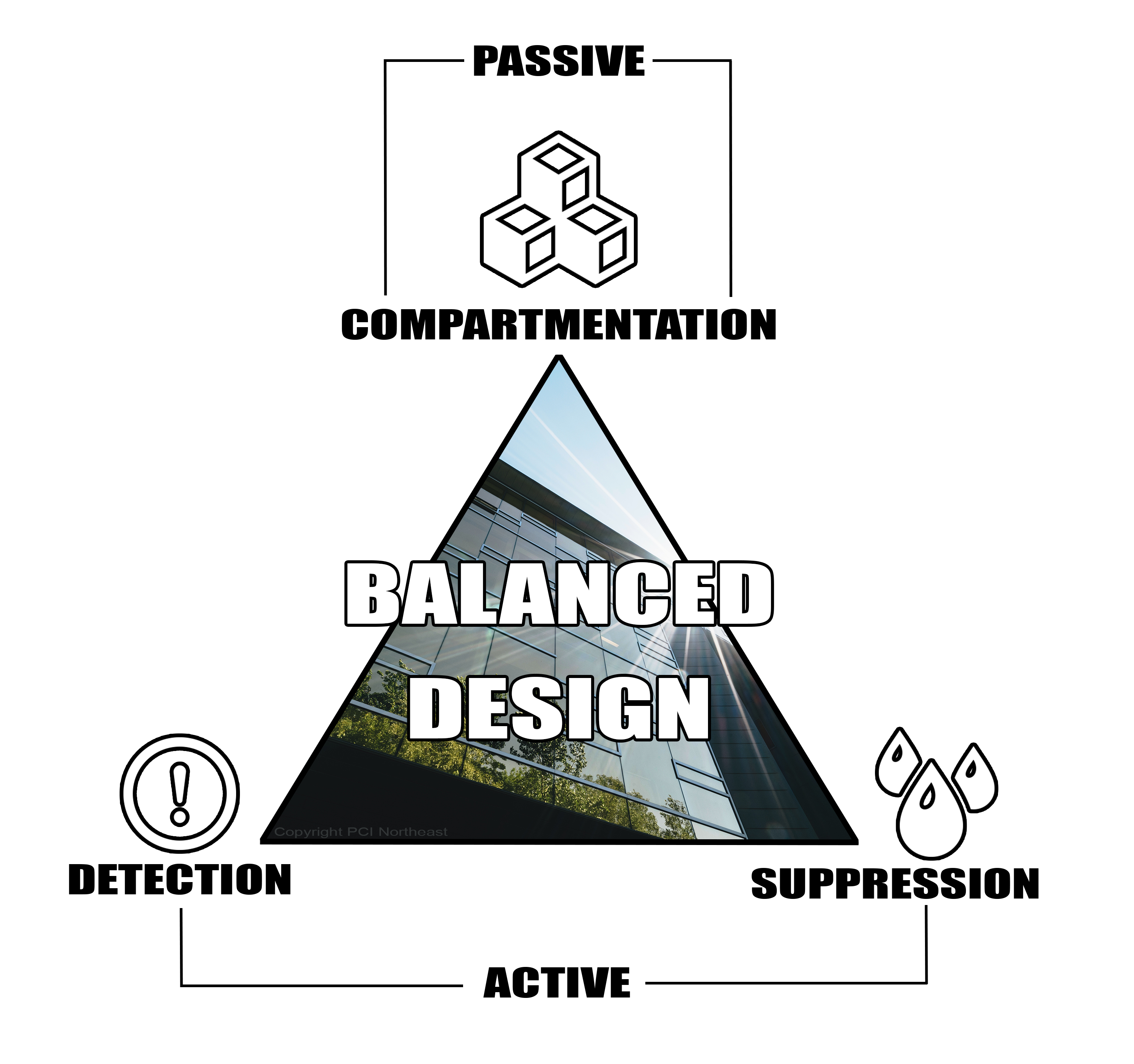
Detection and Suppression design elements are active systems which require an input to operate properly such as a water source or electric.
Compartmentation is a passive system that does not require any outside force to be active. If a fire starts in a room or compartment of a building and compartmentation design was used to create separate areas with concrete walls, the fire could be contained with passive protection from the surrounding structural elements like the walls and ceiling.
Balanced design uses both active and passive design elements to keep the spread of fire events contained allowing firefighters time to arrive and put out the flames while minimizing damage to the structures and potentially saving lives.
Precast Cost Comparison to Wood
In 2017, the Pennsylvania Concrete Masonry Association published an update to the original study of
Initial Cost of Construction for Multi-Residential Structures Their goal was to show the industry that concrete products were not extremely more costly than wood as is the common misconception.
What they found was that, depending on region, the cost of building with precast was actually lower than using conventional wood framing.
Below is a look at 2 locations in the state of New York. While precast was found to be slightly more costly than wood in that region, the benefits of using precast such as mold resistance and minimal damage in a fire event could actually save building owners' in future maintenance costs.
Fire Resistant Precast Components
There are a variety of precast components that can be used to achieve passive-design systems for multi-residential buildings such as hollow-core slabs and precast walls which service as combined floor/ceiling/wall systems.
Don’t forget to check out PCI NE’s Fire Resistance resources to learn more about precast and how it can provide fire resistance to your next project.
Precast vs Fire Case Study
The Forest House apartments in New York is an eight-story, 124-unit residential apartment structure that features precast concrete load-bearing architectural walls embedded with thin brick, hollowcore plank, and other precast concrete pieces, including stairs and landings, lintel beams, and parapets
The design included insulated precast concrete walls which not only supplied high energy efficiency, but also passive fire resistance. The precast’s inorganic composition, which included fly ash to reduced cement requirements, will aid in the buildings fire resistance and minimize the fire spread allowing more time to contain it.
Learn more about this multi-residential building and its precast fire resistance.
Conclusion
Through the use of balance design and material like precast concrete, buildings can be constructed to better handle fire events without costing a fortune. It’s easy to see why precast concrete makes sense for long-term performance of multi-residential applications.
Need to find out if precast is right for your next project? Try our Solution Center and get cost information directly from PCI Northeast producers.